About Keteer Mould
Foshan Keteer Plastic Mould Co., Ltd was established in 2007, with over 15 years of plastic injection molding experience, Keteer Mould has grown to be recognized as a global leader in custom plastic injection molding. Partnering with OEM enterprise worldwide, in a wide range of industries.
In Keteer Mould we have more than 100 manufacturing personnel including project manager, professional mold designers, engineers, and product developers.
We can design and mold custom plastic parts and assemblies that enhance end products, to help customer reduce overall part and production costs, and streamline assembly and manufacturing processes.
We are cooperating with many clients all over the world, such as famous household appliance brand Midea; TCL; Hisense; Chigo etc.
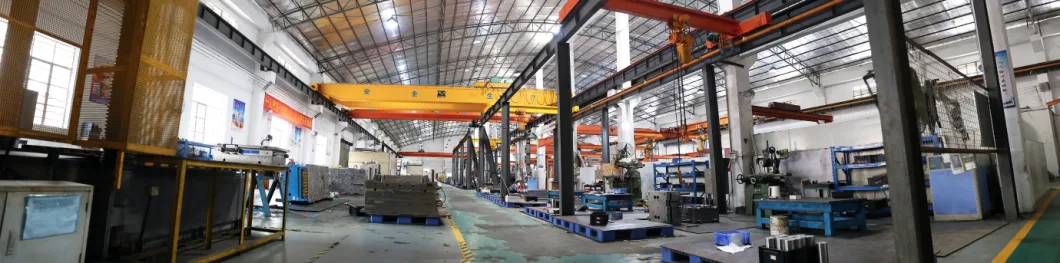
Plastic Injection Molding Manufactures Form China
In Keteer Mould, we can design and mold custom plastic parts and assemblies that enhance end products, to help customer reduce overall part and production costs, and streamline assembly and manufacturing processes.
Keteer believes our true success comes only from an approach and commitment to plastic injection molding that provides each customer unparalleled competitive advantage in terms of improved quality, appeal, efficiency and increased profitability.
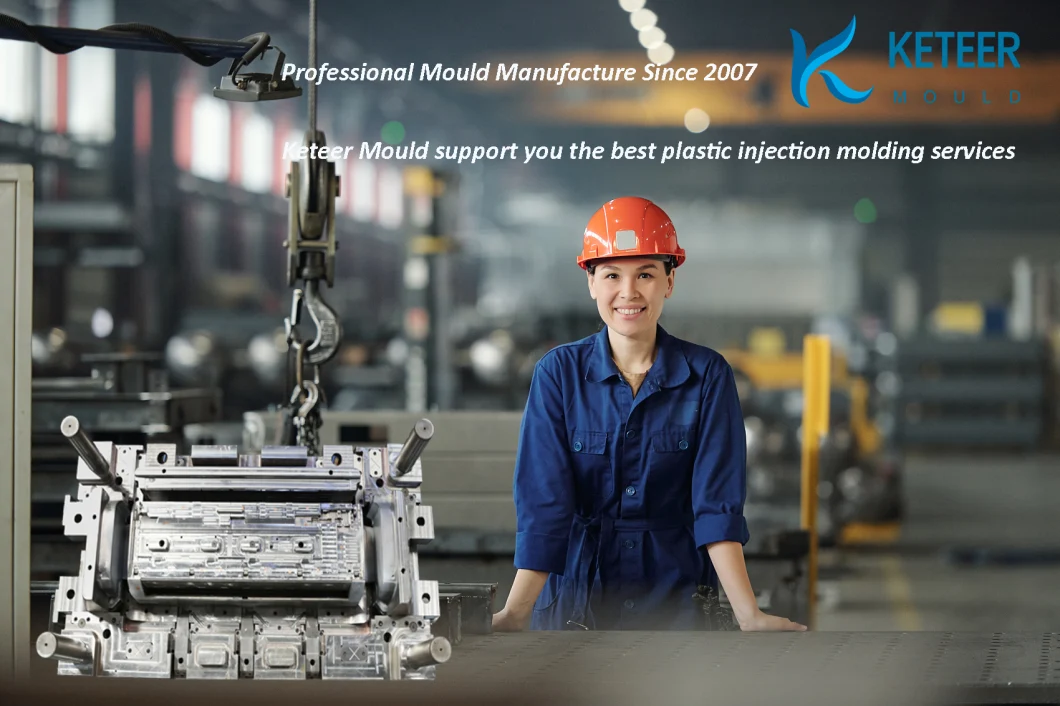
Water Appliances Plastic Mold
In Keteer Mould, we specialize in research and the development, production, and sales of many type of water appliances plastic components cover mold, such as: water purifiers, water heater, water dispenser, and commercial type water dispensers and purification equipment etc.
If you are looking for design or development water purification or heaters, we have professional engineers and mould design team to suit your needs!
We are the one of largest water appliance molding manufacturer in the world, but we are also growing to reach the best of the China and international standard for injection molding.
Basic Information:
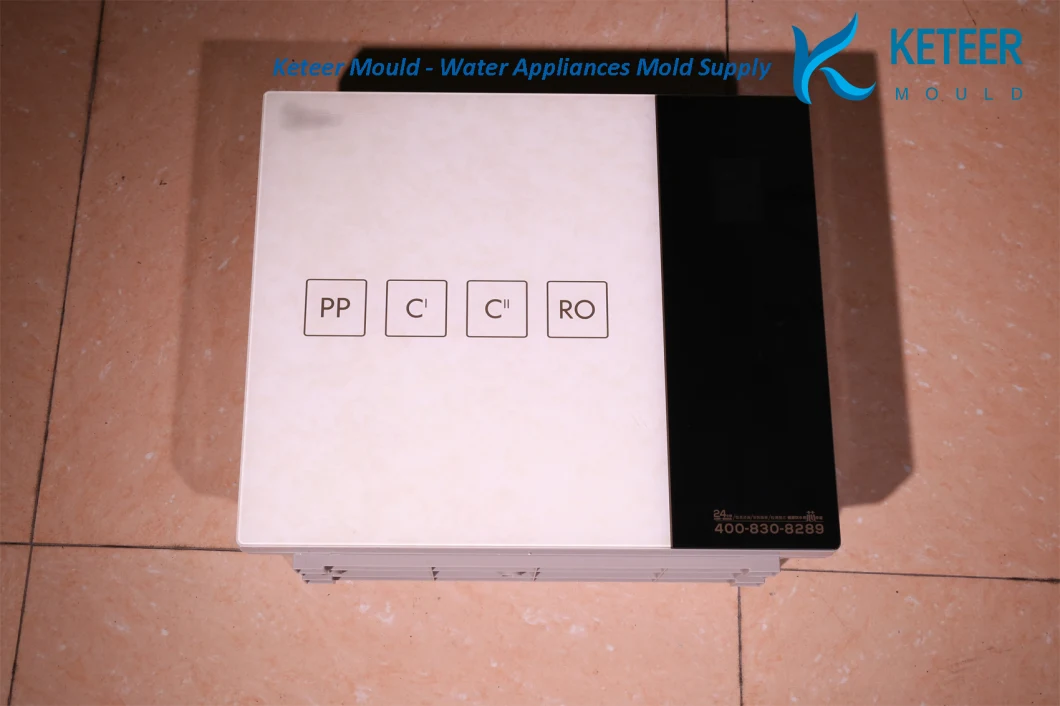
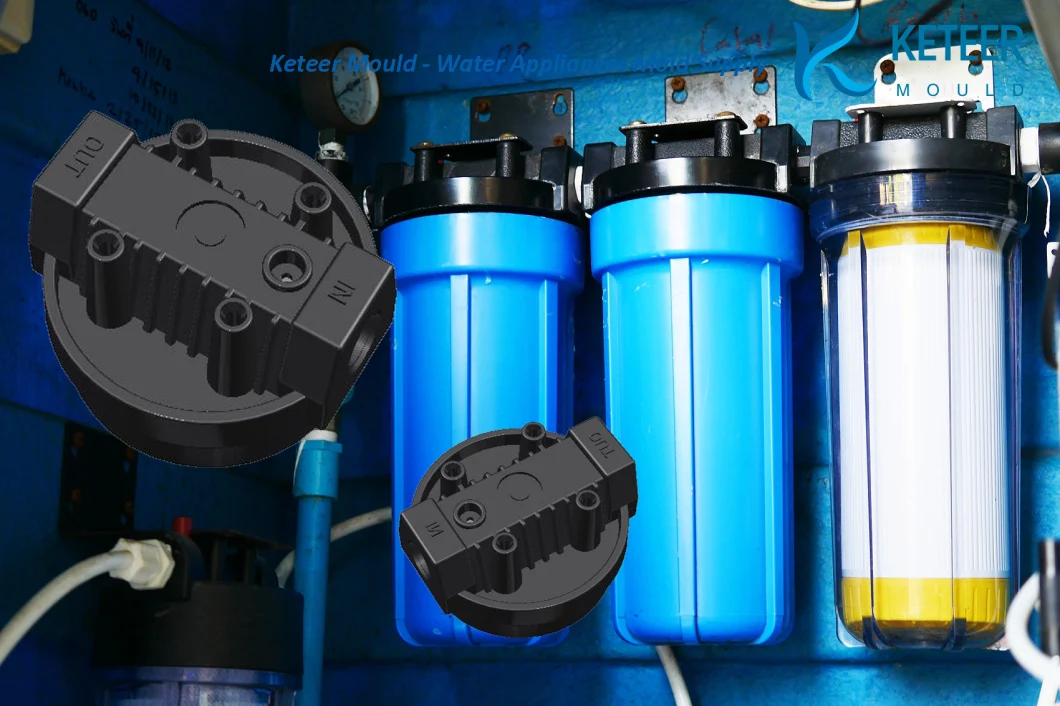
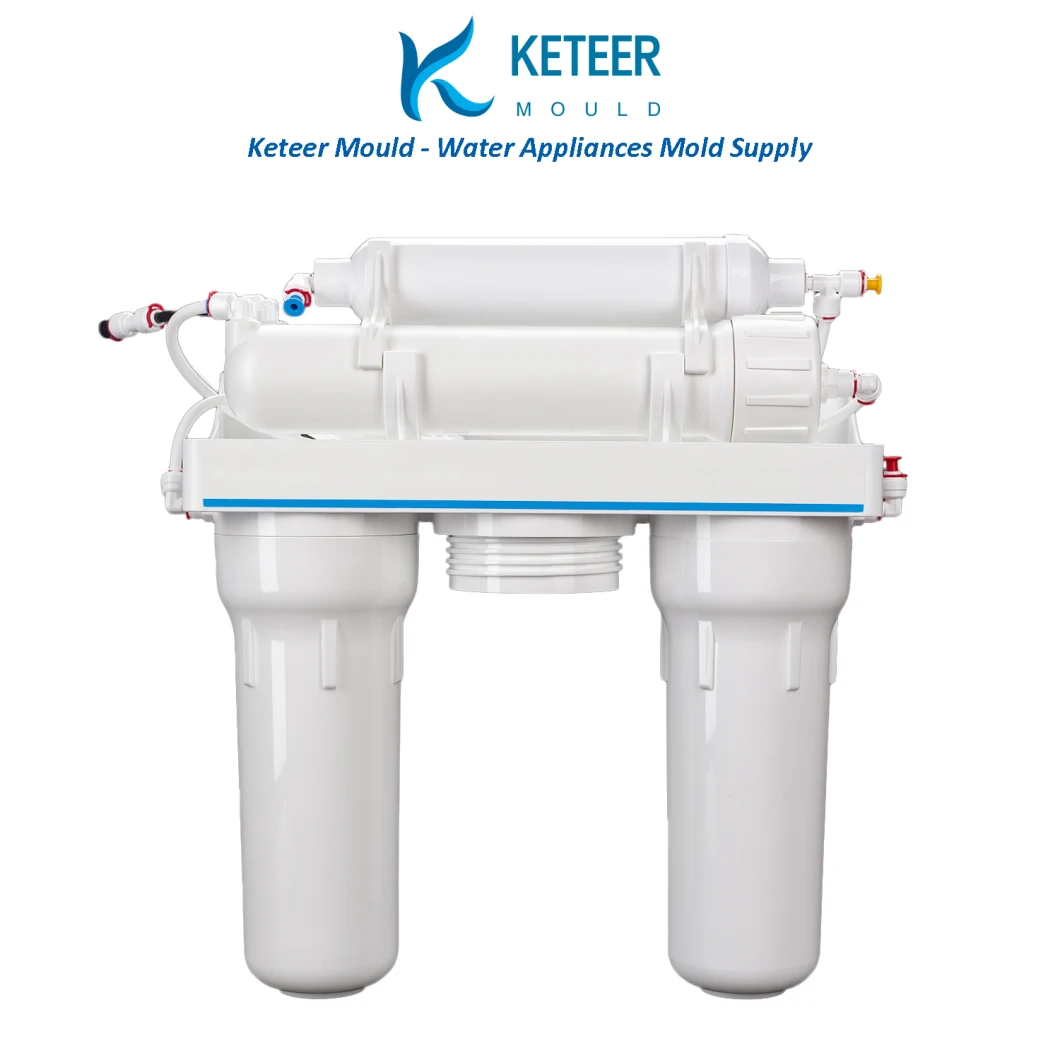
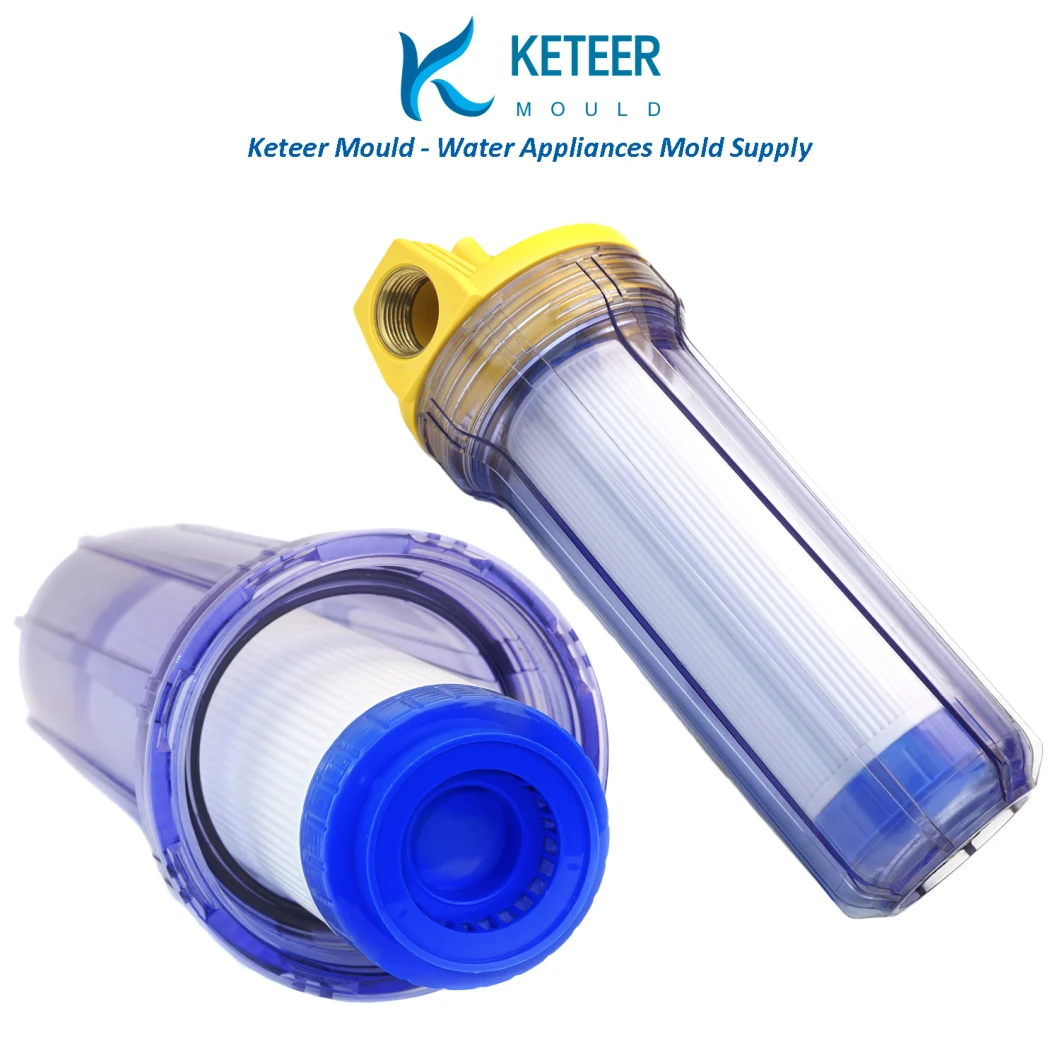
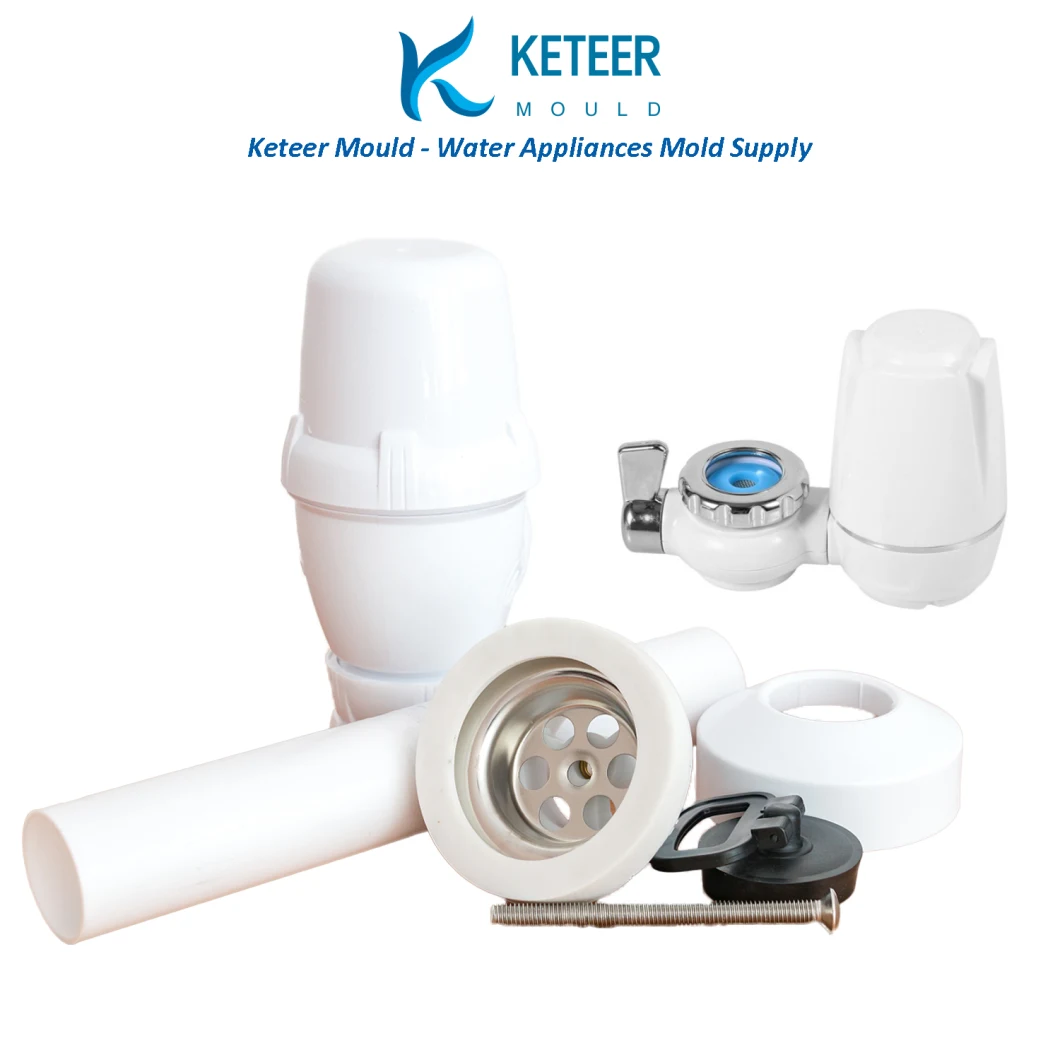
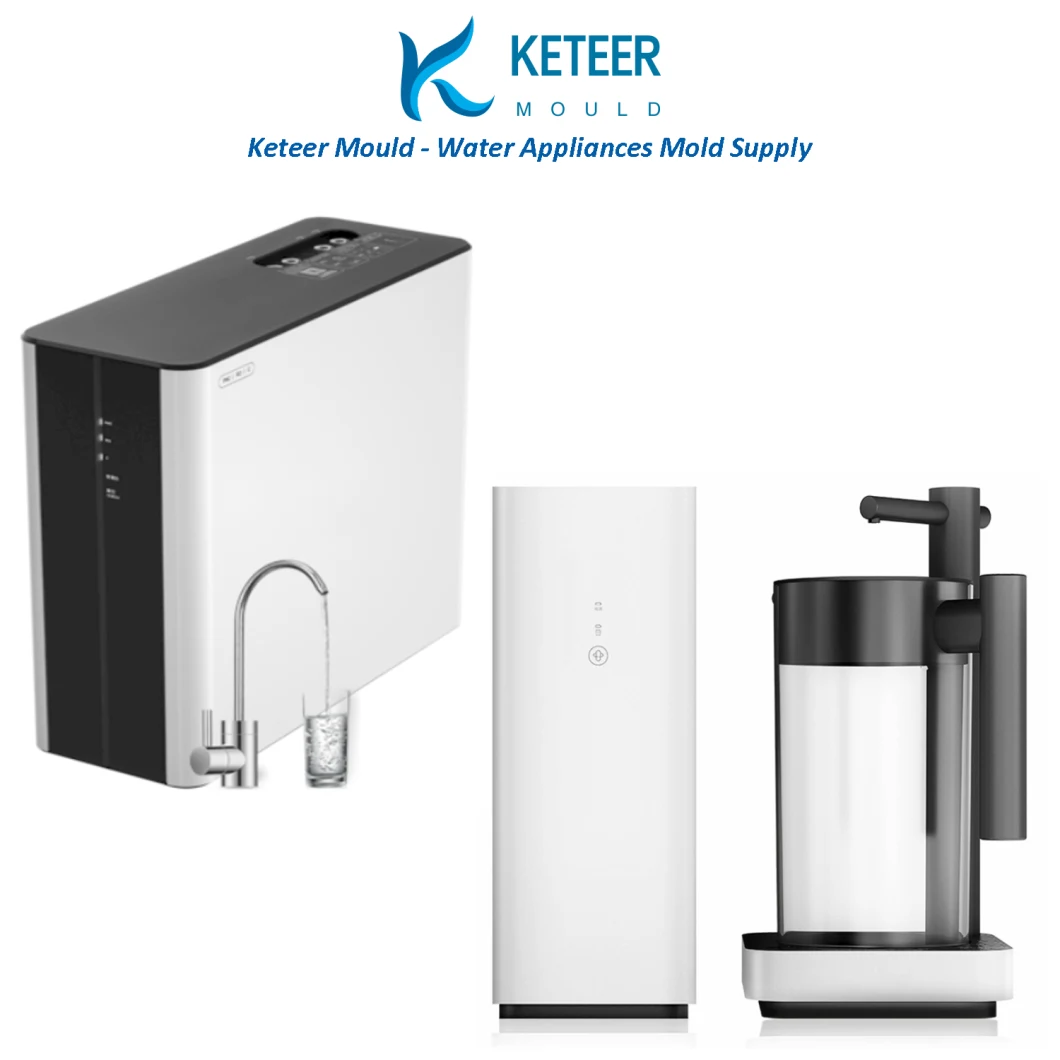
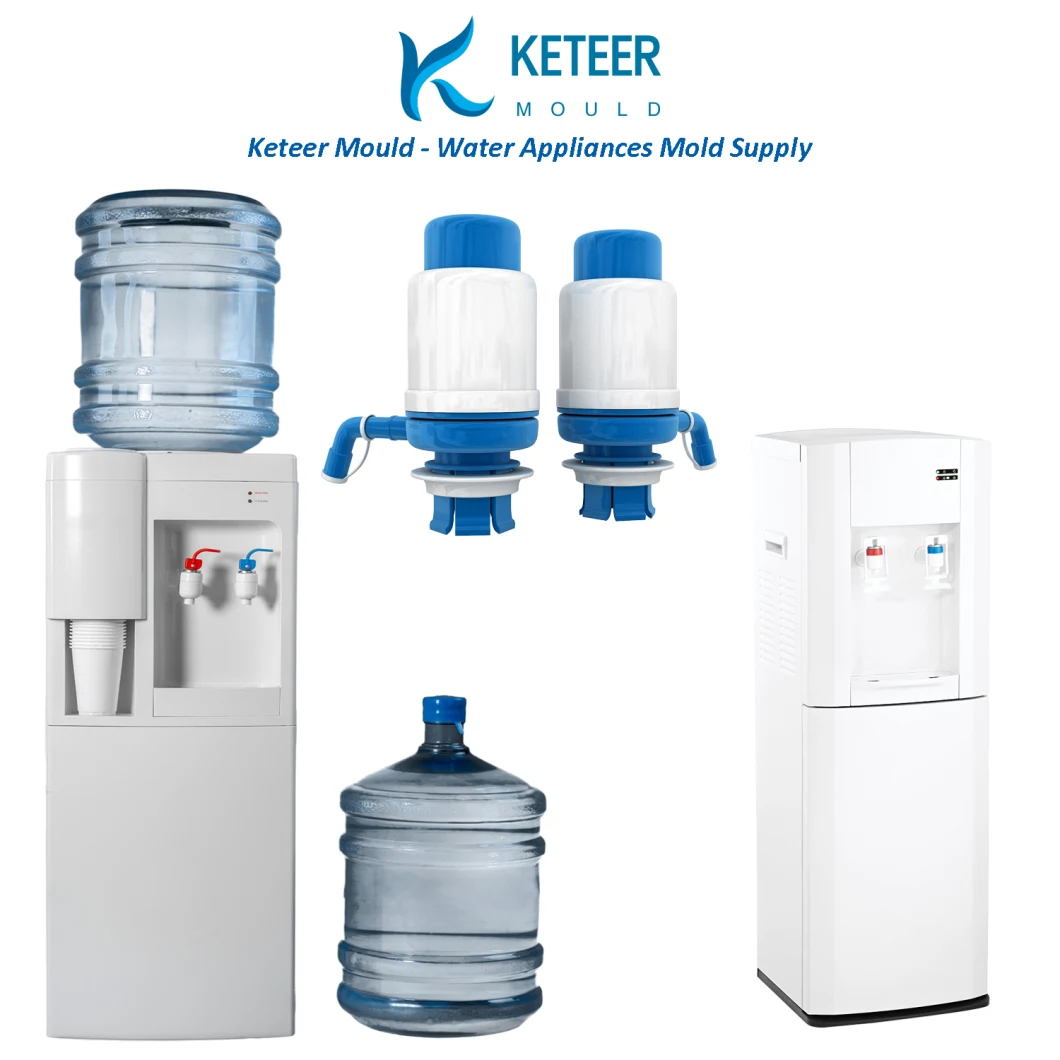
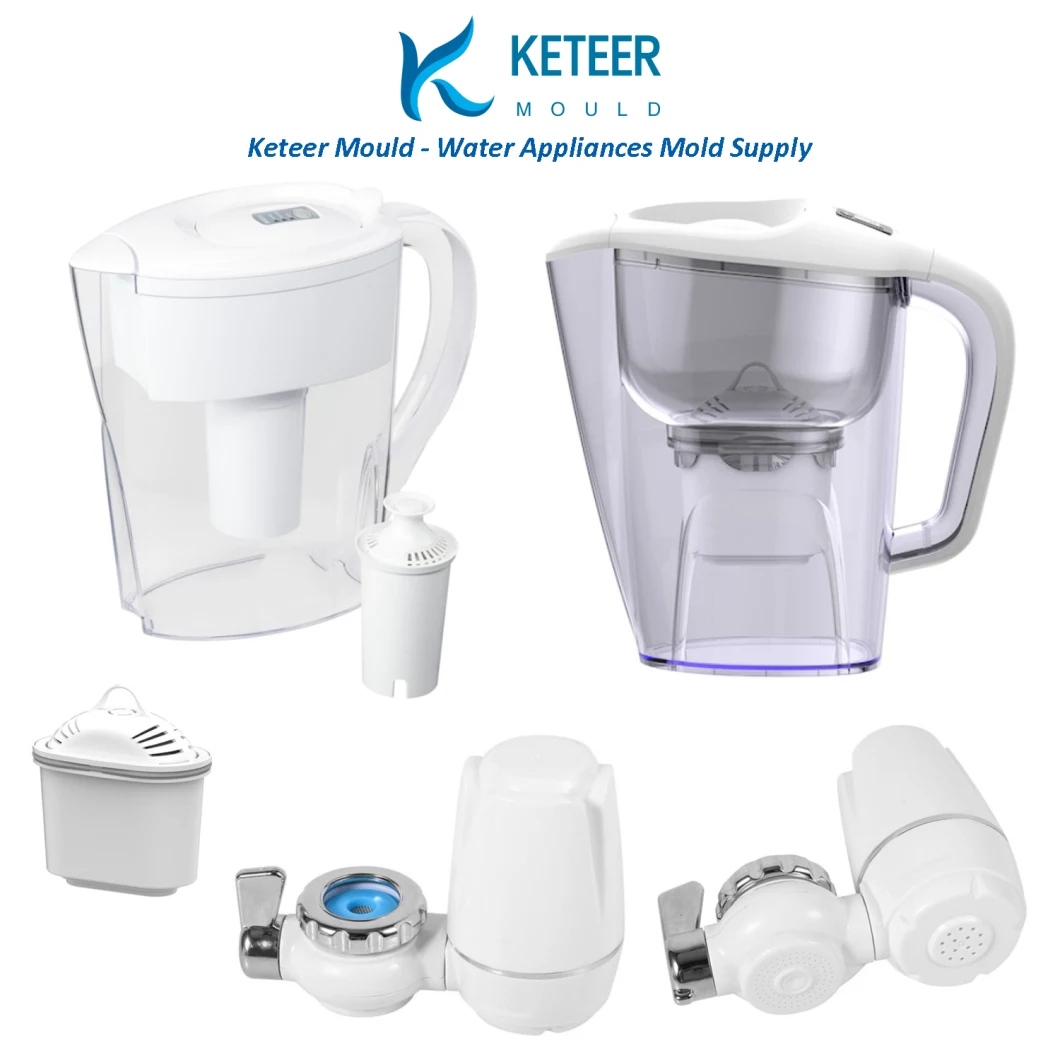
Injection Molded Part Design Service
Keteer Mould provides professional plastic injection mold tool design services as DME or HASCO standard for customers in 2D or 3D CAD files.
In Keteer Mould design services team have more than 10 engineers, and have 6 senior injection mold tooling engineers. Our engineers can design injection molds from basic single cavity prototype to complex, multi-cavity long life production molds.
In order to design an injection molded part that meets your needs, our engineers will help you to select an appropriate plastic material, develop a functional design, and work within the manufacturing limitations associated with the injection molding process.
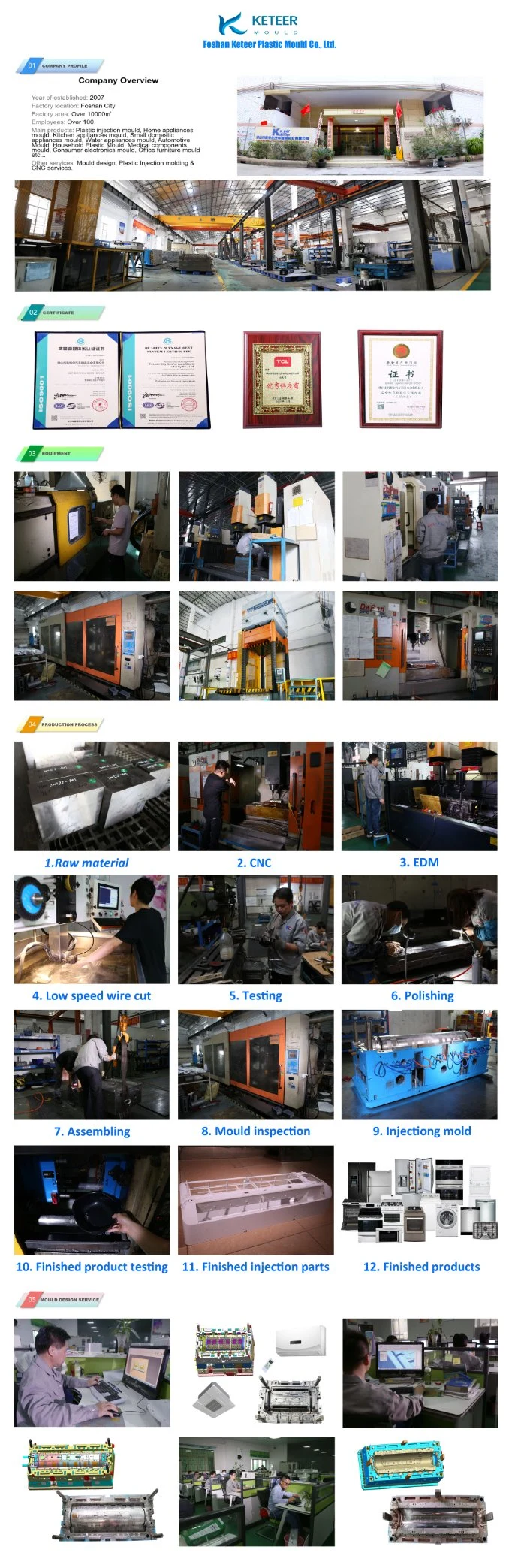
Why Choose Keteer Mould? What is the Benefits?
Design team and manufacturing
We don't just offer injection molding services, but all-in-one design team and manufacturing services. We can help you build a prototype part, refine your design, choose the right plastic resin for your needs, and manufacture your molds and your products - all in the same facility!
This saves you time and money, since there's no need to work with any other third parties to build your components. We can handle the entire process in-house at our facility, ensuring that you get the plastic injection-molded parts you need quickly and at a low cost.
Professional Advanced Machines
We have invested heavily in the latest modern injection molding machines. Our injection molding machines provide more consistent results and higher efficiency - at a lower cost
We pass these savings on to our customers, allowing them to get the plastic injection-molded
Keteer Mould - Your Direct Manufacturing
Unlike some other companies out there, we are not a middle-man. We do not contract your parts out to other third-party manufacturers and take a cut of the profit for ourselves
Instead, we handle every step of the manufacturing process in-house. By doing so, we can ensure that your product quality is absolutely perfect - and minimize the risk of faulty or improperly-molded parts. This, in turn, saves you both time and money
WHY US? Why Choose Keteer Mould?
a. Guaranteed Quality Plastics
b. Excellent Customer Service
c. Rapid Turnaround Time
d. Mold-Flow Analysis Software
e. Exact Color Match
f. Operations Management
g. Logistics Management
h. Product Assembly
i. Product Packaging
j. Order Fulfillment
k. Drop Shipping
l. Contract Manufacturing
FAQ
Common Question About Plastic Injection Molding
Q: Causes and solutions for product burrs(flash) formed when the injection machine first starts, as well as an incomplete filling after a while of production:
A: When the machine first starts, the melting in the injection machine barrel flows smoothly with a lower stickiness thanks to a longer period of heating, so product burrs tend to occur. After a while of production, since the melting continuously takes the heat away, the product will not be fully injected due to great stickiness and poor liquidity. This problem can be solved by gradually increasing the temperature of the barrel after some time into the production.
Q: In the production process, the product cannot be fully injected, even increasing injection pressure and velocity won't work sometimes. Why and how to solve it:
A: In the production process, the melting continuously takes the heat away, so the product will not be fully injected due to great stickiness and poor liquidity. This problem can be solved by increasing the temperature of the injection machine barrel.
Q: Causes and solutions for product becoming oval:
A: A product becomes oval is because the melting is not evenly fed, causing uneven pressure on the circumference of the product thus making it oval. The 3-point injection approach can be adapted to allow for even feeding.
Foshan Keteer Plastic Mould Co., Ltd was established in 2007, with over 15 years of plastic injection molding experience, Keteer Mould has grown to be recognized as a global leader in custom plastic injection molding. Partnering with OEM enterprise worldwide, in a wide range of industries.
In Keteer Mould we have more than 100 manufacturing personnel including project manager, professional mold designers, engineers, and product developers.
We can design and mold custom plastic parts and assemblies that enhance end products, to help customer reduce overall part and production costs, and streamline assembly and manufacturing processes.
We are cooperating with many clients all over the world, such as famous household appliance brand Midea; TCL; Hisense; Chigo etc.
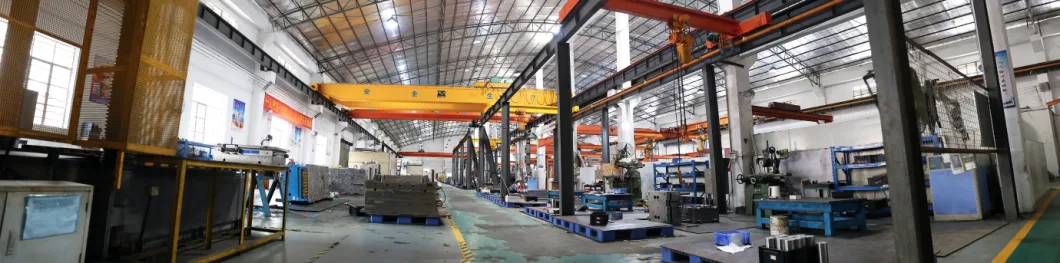
Plastic Injection Molding Manufactures Form China
In Keteer Mould, we can design and mold custom plastic parts and assemblies that enhance end products, to help customer reduce overall part and production costs, and streamline assembly and manufacturing processes.
Keteer believes our true success comes only from an approach and commitment to plastic injection molding that provides each customer unparalleled competitive advantage in terms of improved quality, appeal, efficiency and increased profitability.
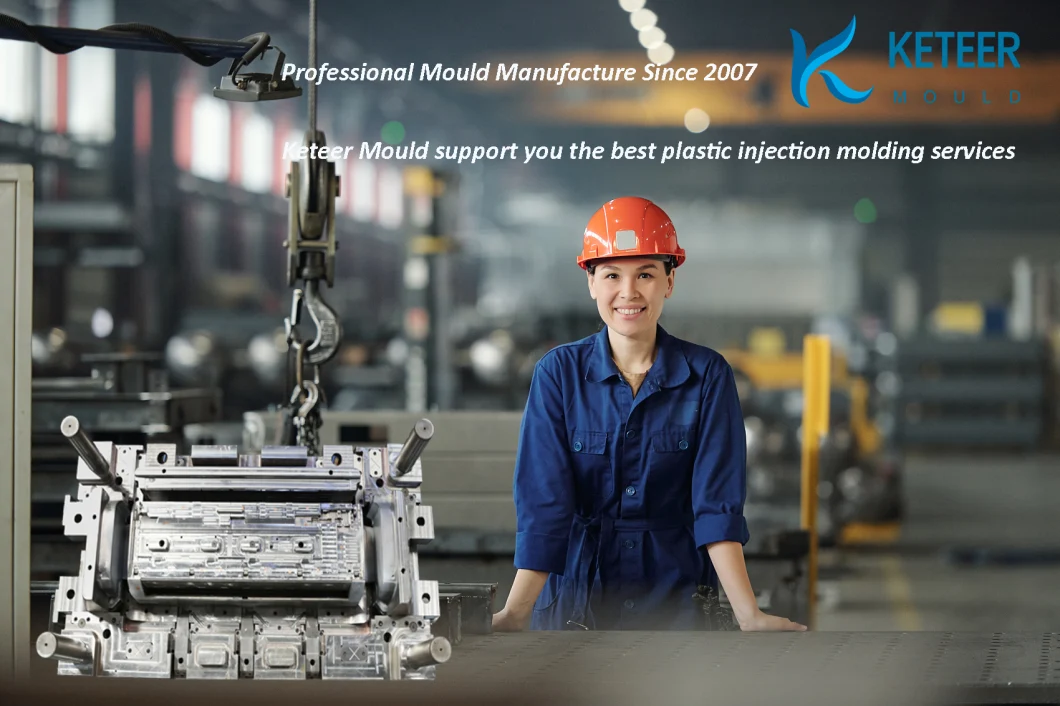
Water Appliances Plastic Mold
In Keteer Mould, we specialize in research and the development, production, and sales of many type of water appliances plastic components cover mold, such as: water purifiers, water heater, water dispenser, and commercial type water dispensers and purification equipment etc.
If you are looking for design or development water purification or heaters, we have professional engineers and mould design team to suit your needs!
We are the one of largest water appliance molding manufacturer in the world, but we are also growing to reach the best of the China and international standard for injection molding.
Basic Information:
Product Name | OEM Customized Plastic Water Purifier Cabinet, Water Dispenser Injection Mould |
Business type | Plastic Mold Manufacturer |
Part Name | Injection Mold |
Main Product | Plastic Injection Mold, Die Casting Mould, Mold design, Home Appliance Mold, Kitchen Appliance Mould, Medical Appliance Mold, Automobile Accessory Mold, Electronic Equipment Mold, Office Equipment Mold, Daily Commodity Mold, Special Structure Mold, Other Injection Mold, CNC Milling,, Injection Molding Product, 2D/3D Printing etc... |
Mould Base | SD,LKM Standard, HASCO Standard Self-made, etc. |
Mould Material | P20/718/738/NAK80/S136/2738/2316/H13, etc. |
Mould Precision | +/-0.01mm |
Mould Life | 50-500K Shots |
Mould Cavity | Single Cavity, Multi-cavity |
Runner System | Hot runner and cold runner |
Gate Type | Pinpoint Gate, Edge Gate, Sub Gate, Film Gate, Valve Gate, Open Gate, etc. |
Equipment | CNC Machine, EDM Machine, EDM Double Head Machine, Low Speed Wire Cut Machine, Middle Speed Wire Cut Machine, Mold Closing Machine, Mold Rotator Machine, 5 set different size Injection Molding Machine, Grinding Machine, Lathe Machine, Milling Machine, Drilling Machine, Laser Welding Machine, Overhead Crane etc.... |
Plastic Material | PA6,PA66,ASA,POM,PPS,ABS,ABS+GF,ABS+PC,POM(Derlin),PP,PE,PC,PMMA(Acrylic),PVC,PEI,PBT,PTFI |
Metal Material | Aluminum(6061,6063,7075...),Brass,Copper,Stainless Steel(301,302,303,304...) |
Surface Treatment | Polishing,Painting,Chroming,Anodizing, Brushing, Silk Screening, Water Transferring, Laser Cutting, Leather Covering, Texture, San blasting, Gilding, UV Painting… |
Please Provide | 2D, 3D, Samples, or the size of the multi-angle pictures |
Quality System | ISO 9001: 2015 |
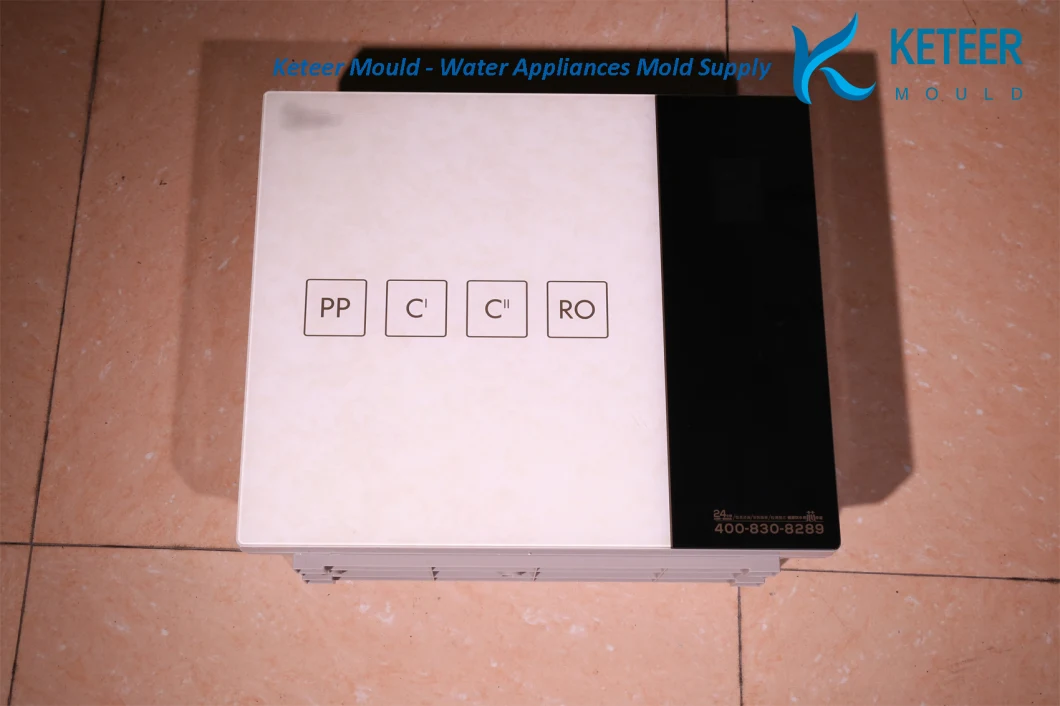
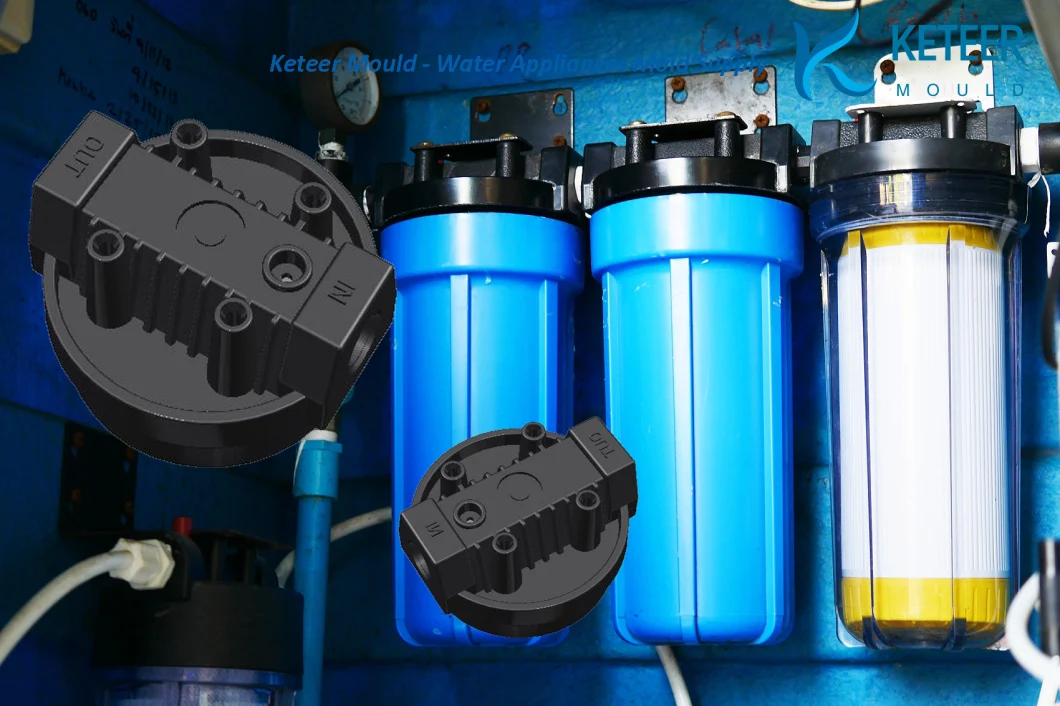
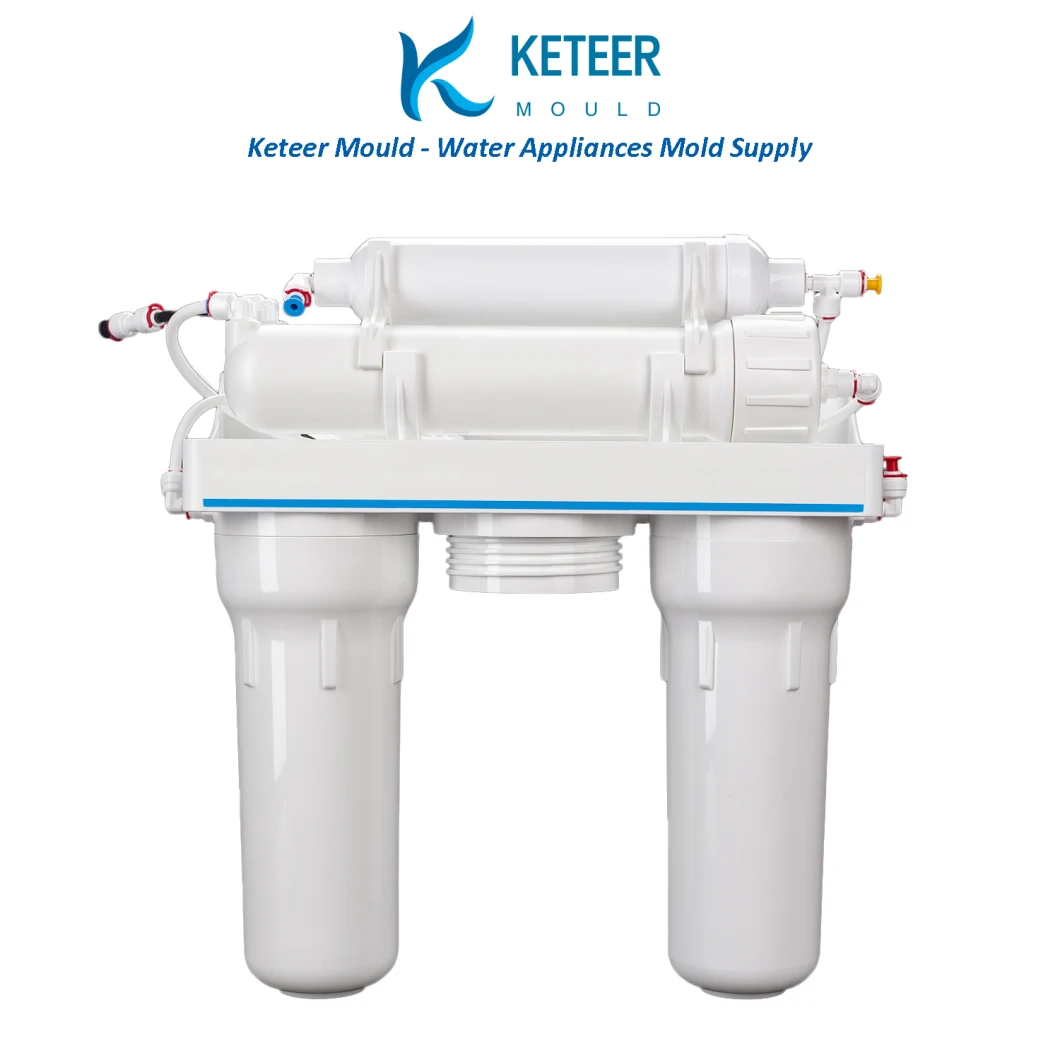
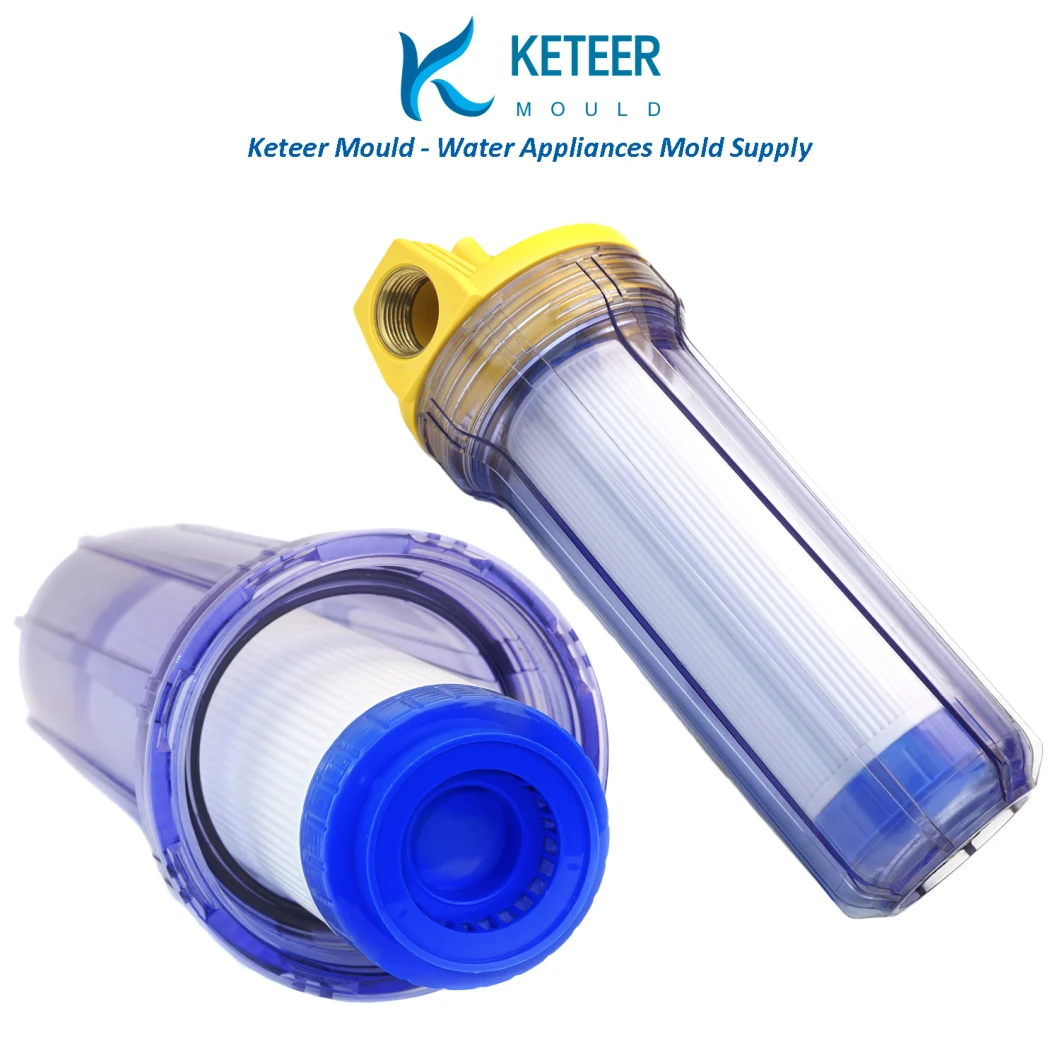
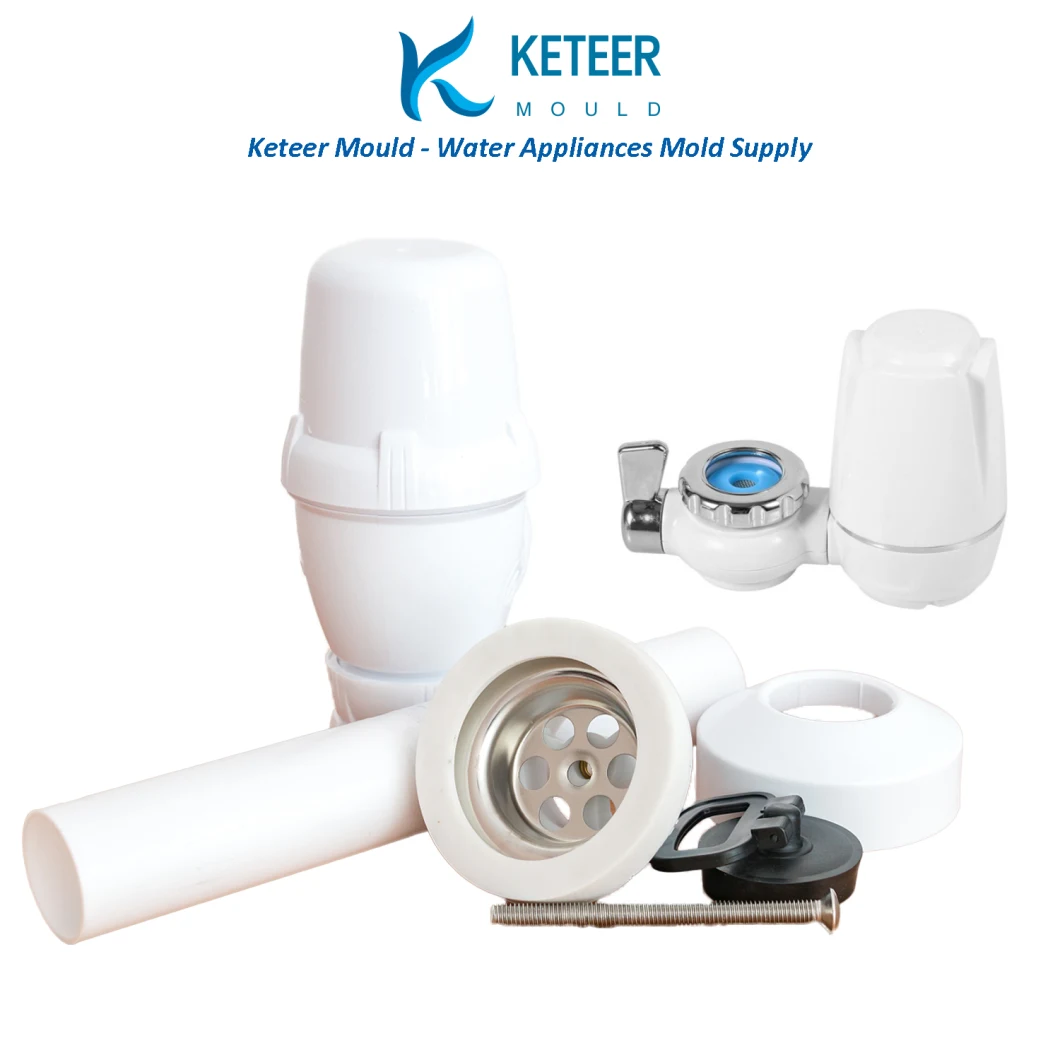
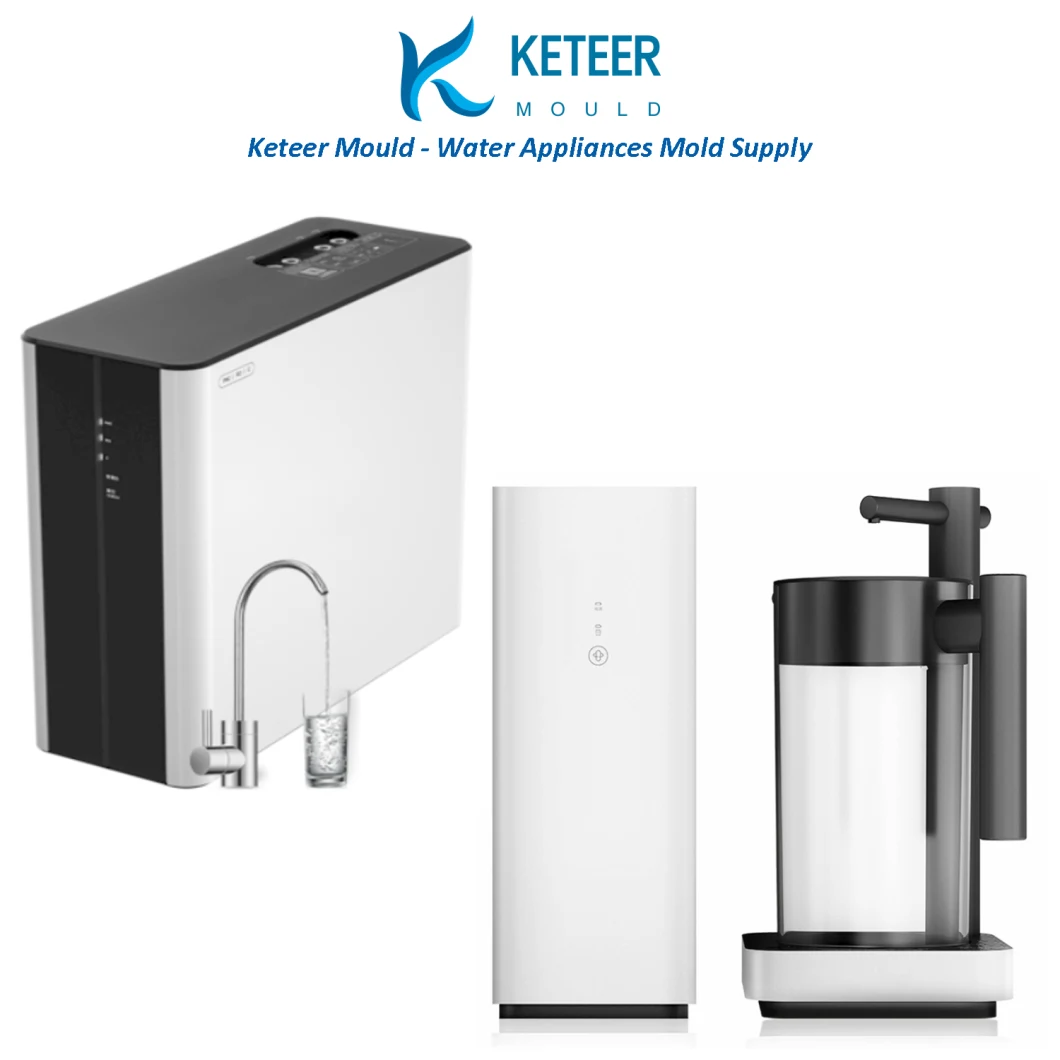
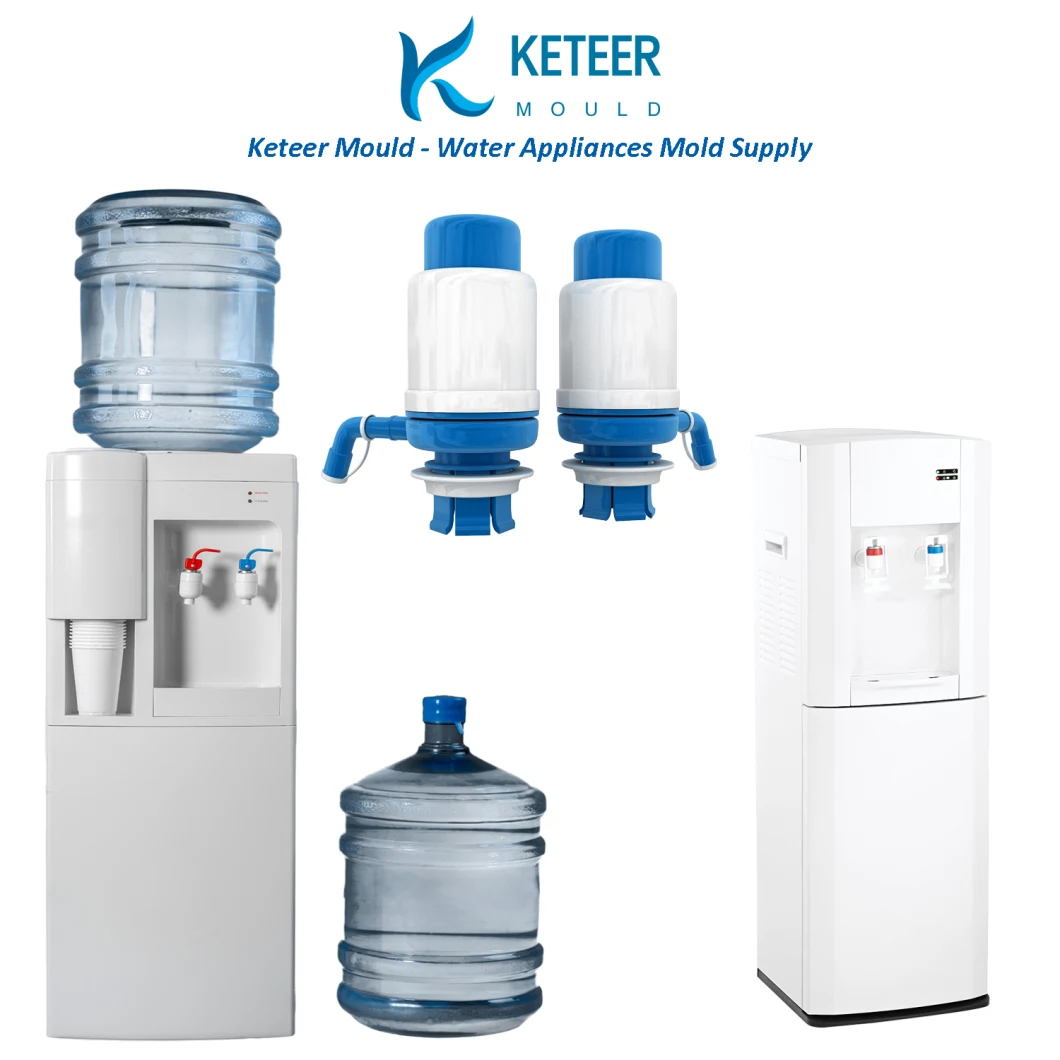
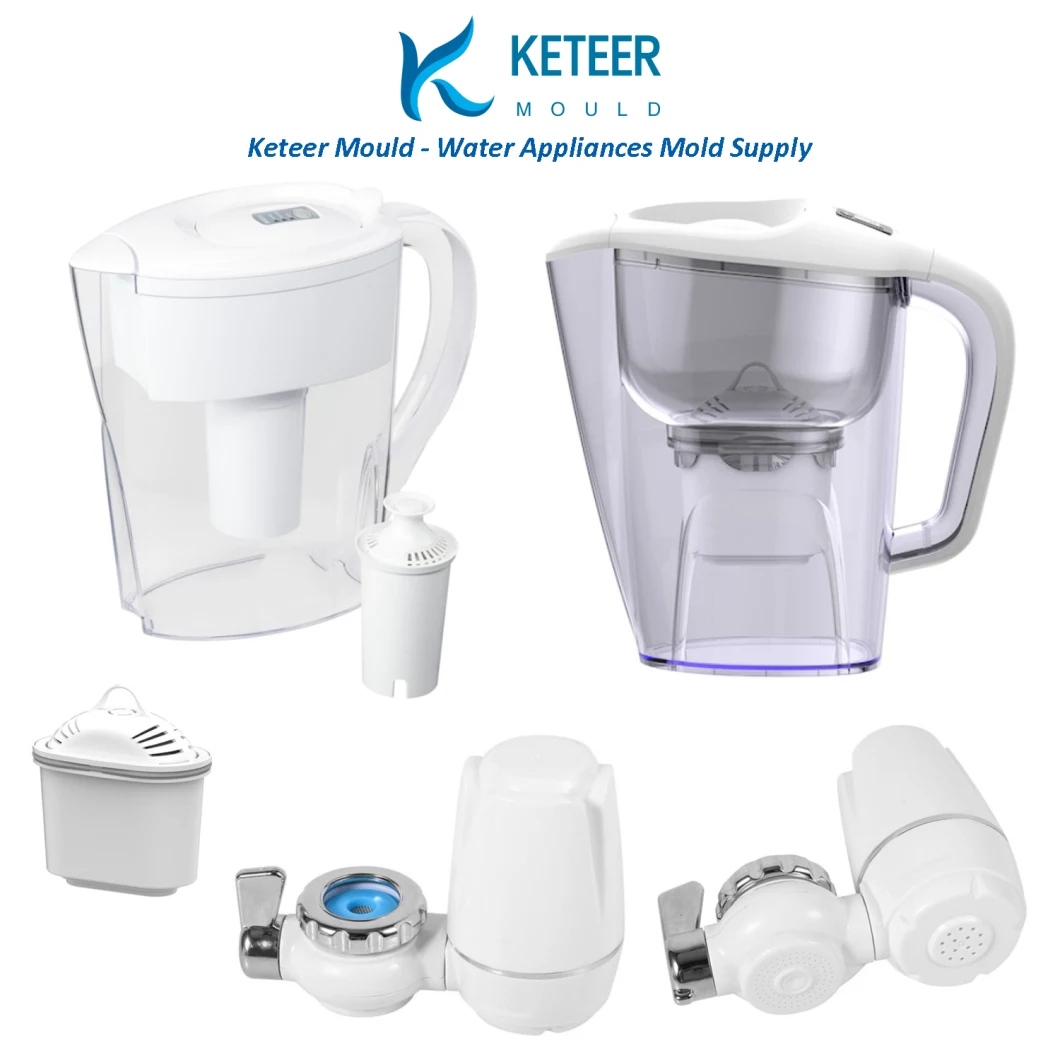
Injection Molded Part Design Service
Keteer Mould provides professional plastic injection mold tool design services as DME or HASCO standard for customers in 2D or 3D CAD files.
In Keteer Mould design services team have more than 10 engineers, and have 6 senior injection mold tooling engineers. Our engineers can design injection molds from basic single cavity prototype to complex, multi-cavity long life production molds.
In order to design an injection molded part that meets your needs, our engineers will help you to select an appropriate plastic material, develop a functional design, and work within the manufacturing limitations associated with the injection molding process.
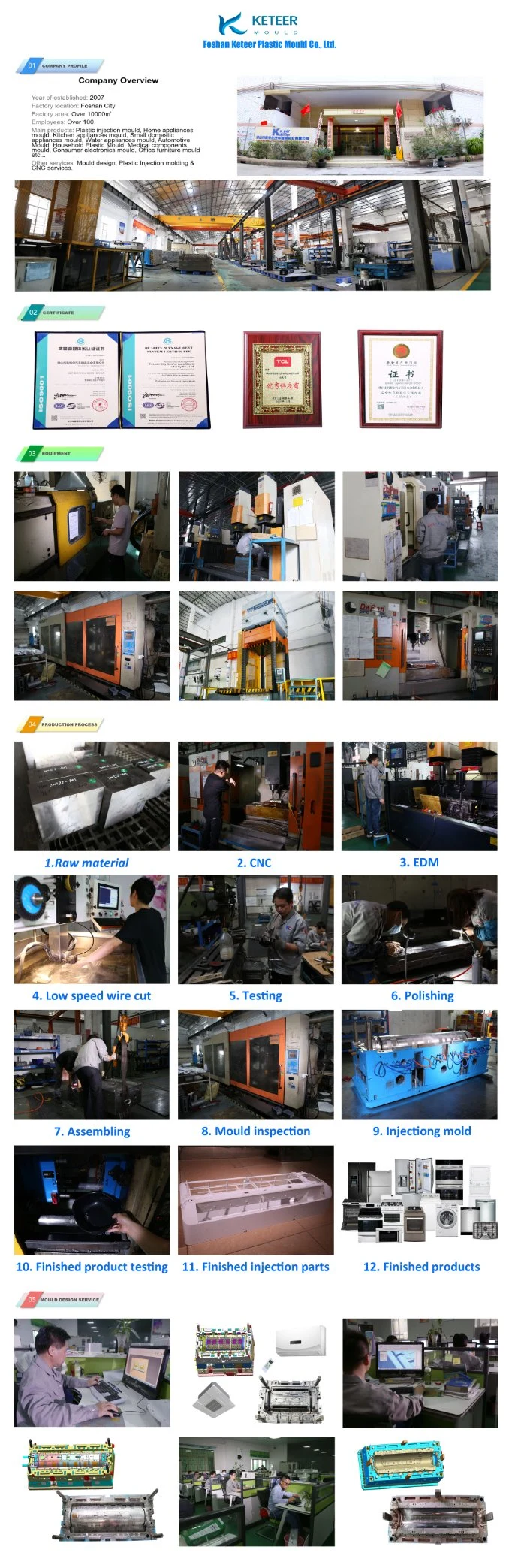
Why Choose Keteer Mould? What is the Benefits?
Design team and manufacturing
We don't just offer injection molding services, but all-in-one design team and manufacturing services. We can help you build a prototype part, refine your design, choose the right plastic resin for your needs, and manufacture your molds and your products - all in the same facility!
This saves you time and money, since there's no need to work with any other third parties to build your components. We can handle the entire process in-house at our facility, ensuring that you get the plastic injection-molded parts you need quickly and at a low cost.
Professional Advanced Machines
We have invested heavily in the latest modern injection molding machines. Our injection molding machines provide more consistent results and higher efficiency - at a lower cost
We pass these savings on to our customers, allowing them to get the plastic injection-molded
Keteer Mould - Your Direct Manufacturing
Unlike some other companies out there, we are not a middle-man. We do not contract your parts out to other third-party manufacturers and take a cut of the profit for ourselves
Instead, we handle every step of the manufacturing process in-house. By doing so, we can ensure that your product quality is absolutely perfect - and minimize the risk of faulty or improperly-molded parts. This, in turn, saves you both time and money
WHY US? Why Choose Keteer Mould?
a. Guaranteed Quality Plastics
b. Excellent Customer Service
c. Rapid Turnaround Time
d. Mold-Flow Analysis Software
e. Exact Color Match
f. Operations Management
g. Logistics Management
h. Product Assembly
i. Product Packaging
j. Order Fulfillment
k. Drop Shipping
l. Contract Manufacturing
FAQ
Common Question About Plastic Injection Molding
Q: Causes and solutions for product burrs(flash) formed when the injection machine first starts, as well as an incomplete filling after a while of production:
A: When the machine first starts, the melting in the injection machine barrel flows smoothly with a lower stickiness thanks to a longer period of heating, so product burrs tend to occur. After a while of production, since the melting continuously takes the heat away, the product will not be fully injected due to great stickiness and poor liquidity. This problem can be solved by gradually increasing the temperature of the barrel after some time into the production.
Q: In the production process, the product cannot be fully injected, even increasing injection pressure and velocity won't work sometimes. Why and how to solve it:
A: In the production process, the melting continuously takes the heat away, so the product will not be fully injected due to great stickiness and poor liquidity. This problem can be solved by increasing the temperature of the injection machine barrel.
Q: Causes and solutions for product becoming oval:
A: A product becomes oval is because the melting is not evenly fed, causing uneven pressure on the circumference of the product thus making it oval. The 3-point injection approach can be adapted to allow for even feeding.